1000 Sq Ft Slab Cost in India: Real Numbers & Tips
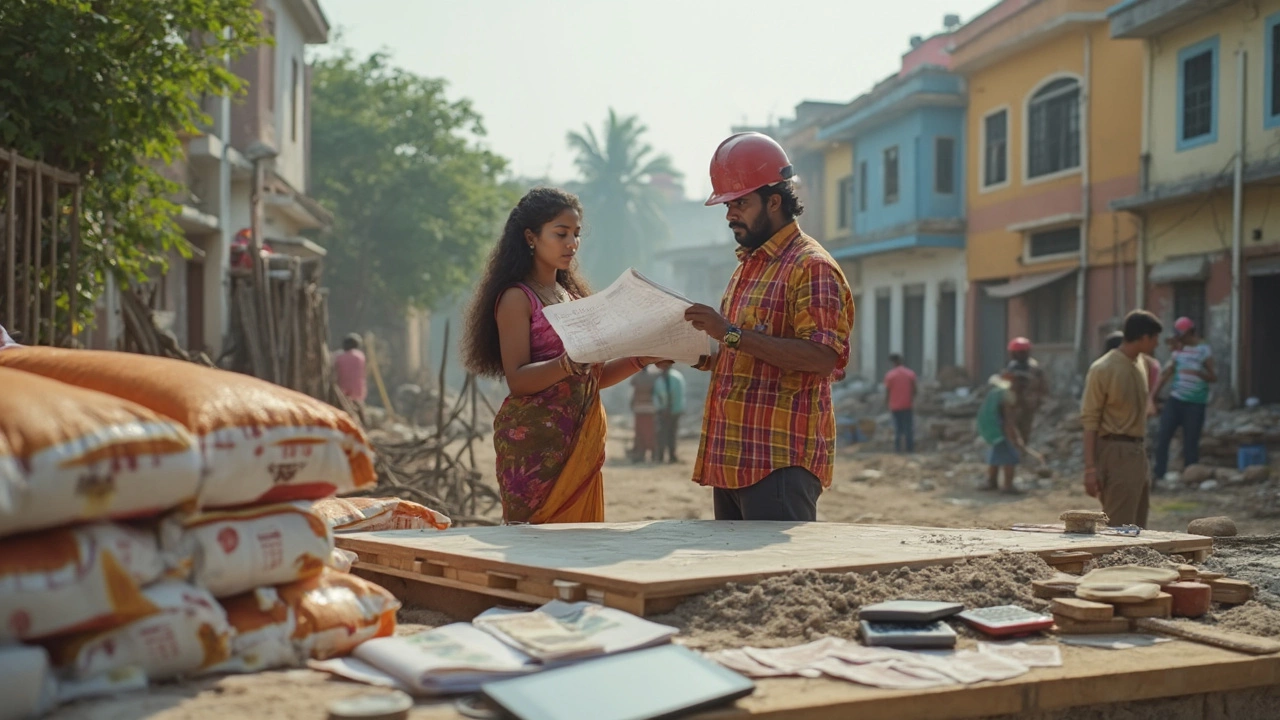
A plain concrete slab underpins your entire studio setup, but getting a straight answer about its cost feels like hunting for a needle in a haystack. If you’re eyeing a 1000 sq ft slab somewhere in India, you’ve got to cut through all the confusion: different material prices, labor rates that jump city to city, and taxes nobody warns you about till you’re signing the check.
Most folks start their budgeting by calling a local mason and asking, “Bhaiya, what will it cost for a concrete slab, 1000 square feet?” Nine times out of ten, you’ll get a vague reply. But the real deal is, the price shifts dramatically depending on where you live, what type of cement and steel you pick, and how strong you need that slab to be.
Don’t just compare numbers from some random Facebook group. Materials have shot up in price lately—cement isn’t what it cost two years ago, and neither is steel. Plus, sand, gravel, and even water charges (yes, really!) sneak into your bill. If you’re figuring costs for your studio setup, keep your eyes open for local rules: some cities slap on extra GST, or want a “permission charge” from the municipality before you can pour the first bucket of mix.
- What Makes Up the Cost of a 1000 Sq Ft Slab?
- Material Breakdown: Cement, Steel, and Beyond
- Regional Variations and Surprise Costs
- Smart Ways to Trim Your Slab Budget
What Makes Up the Cost of a 1000 Sq Ft Slab?
When you ask about the 1000 sq ft slab cost in India, you’re really asking about a combination of several things. The total expense isn’t just about cement and sand—it covers way more ground.
- Materials: This is the big one. Everything from cement, steel, sand, gravel, bricks (for shuttering), and even water adds up. The concrete mix (often M20 grade for most studios) needs the right ratio, or your slab won’t last. Typically, for a slab this size, expect to need around 220-250 bags of cement and 1.5-2 tons of steel.
- Labor Charges: You can’t skip on labor. Masons and helpers charge by the square foot, and the rates can double if you’re in Mumbai compared to a small town like Lucknow. Right now, it could range from ₹30 to ₹75 per square foot just for laying the slab, depending on the city.
- Formwork/Shuttering: Wood or steel plates hold the wet concrete in place until it dries. Renting shuttering adds a surprising chunk—about ₹10-₹20 per sq ft—to your bill.
- Miscellaneous Fees: There’s always a bit extra you don’t plan for: municipal permissions, GST on materials (usually 5%-18%), transport charges if your site is outside city limits, and sometimes even a charge for water if the contractor supplies it.
Component | Typical Cost (per sq ft) |
---|---|
Materials (Cement, Steel, Sand, Gravel) | ₹60 - ₹90 |
Labor | ₹30 - ₹75 |
Shuttering Rent | ₹10 - ₹20 |
Extra Fees (GST, transport, water) | ₹10 - ₹20 |
So, when you calculate the total studio setup cost for a 1000 sq ft slab, you’re usually looking at anywhere from ₹110,000 to ₹200,000. The wide range is all about materials, city, and even who you know. If you’re aiming for premium quality or want to use ready-mix concrete (RMC), costs go higher but save you time and hassle.
One good tip: Always ask your contractor for an all-inclusive quote in writing. Make sure it lists each component clearly—the fastest way to avoid nasty surprises halfway through.
Material Breakdown: Cement, Steel, and Beyond
Let’s break down what really eats up your budget when building a 1000 sq ft slab for your studio. The big three—and you can’t skip these—are cement, steel, and sand. If you’re planning a slab for medium loads (say, music studio equipment), you’ll likely go for the M20 or M25 concrete mix. Here’s where your money goes and why it matters.
Cement takes the largest chunk. For a 1000 sq ft slab, at 5 inches (125mm) thick, you’ll need about 125–130 bags of cement. Right now in India, a bag of OPC 53-grade cement is selling for ₹430–₹500, depending on the city. If you’re near a factory or port, you’ll probably pay less. Your total cement bill? Around ₹55,000–₹65,000 just for those bags.
Next, steel reinforcement (rebar) isn’t negotiable. For slabs, the typical steel requirement is about 3.5–4 kg per sq ft. So, for 1000 sq ft, you need 3.5–4 tons. At today’s average steel price of ₹55–₹67 per kg, your steel cost will swing between ₹1,90,000 and ₹2,60,000. Avoid cheap, low-quality steel; it’s just not worth the headache later.
Sand and coarse aggregate (gravel) flow in next. For a slab this size, you’ll use roughly 70–80 cubic feet of sand and the same for aggregate. Quality river sand is currently going for ₹40–₹55 per cubic foot in cities, sometimes higher during monsoon or if you’re far from sourcing points. Aggregate sits a bit lower, but freight can burn a hole if your site is remote.
Here’s a no-nonsense table showing the latest ballpark rates for a 1000 sq ft slab:
Material | Average Quantity | Current Rate | Estimated Cost (₹) |
---|---|---|---|
Cement | 125 bags | ₹450/bag | 56,250 |
Steel | 3.7 tons (3,700 kg) | ₹62/kg | 2,29,400 |
Sand | 75 cu.ft | ₹50/cu.ft | 3,750 |
Aggregate | 75 cu.ft | ₹45/cu.ft | 3,375 |
Don’t forget water, admixtures (if your engineer suggests any for durability), and the cost of formwork (shuttering wood or plates). Water usually seems trivial, but truckloads can add up to ₹1,000–₹2,000 by the end. Wooden shuttering for a 1000 sq ft slab generally costs around ₹25,000–₹35,000, factoring in labor charges for both setting and removing it. It’s not glamorous, but it’s 100% essential—don’t cheap out on this step or your slab’s finish will haunt you.
- If you’re building in a spot with salty groundwater, add the cost of chemical admixtures. Saves trouble later, even if it pinches now.
- Always check for builder bulk discounts—sometimes dealers offer deals if you buy cement and steel together.
- Keep some buffer: sudden price hikes happen fast. Plan at least 10% extra in your material budget for your studio setup cost.
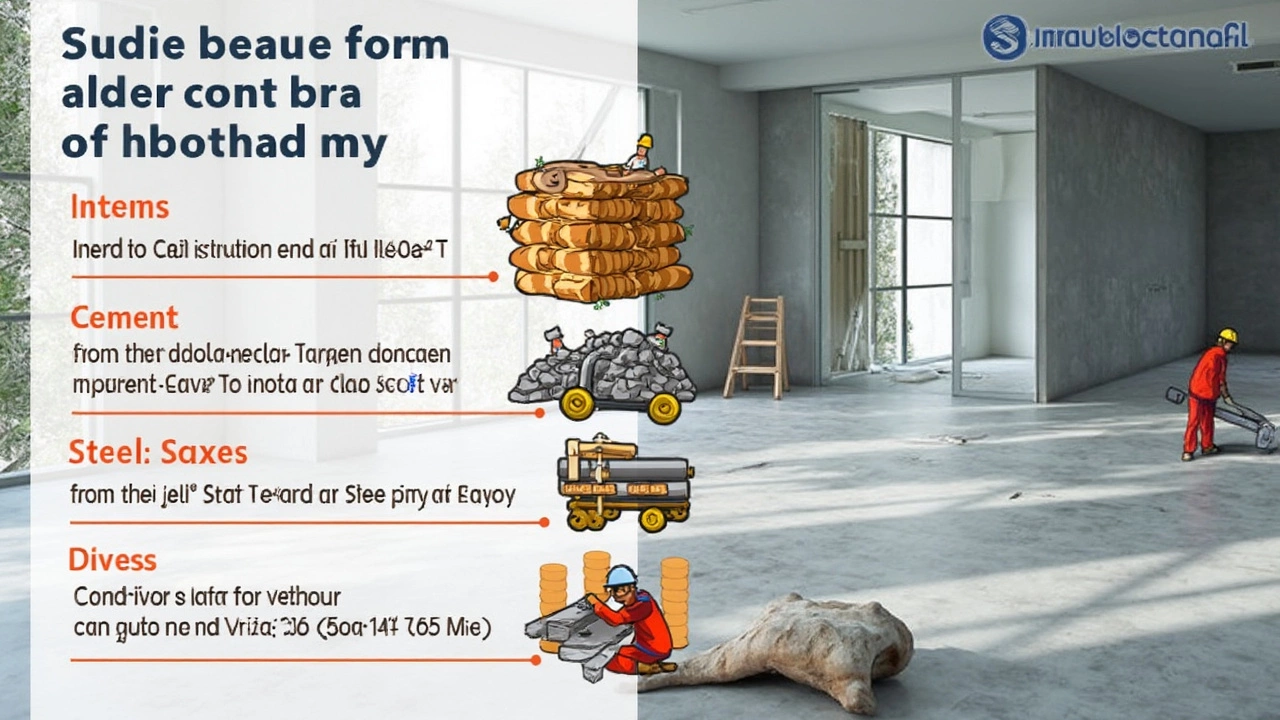
Regional Variations and Surprise Costs
It’s wild how much the 1000 sq ft slab cost can swing from one city to the next. For example, putting down a slab in Bengaluru can cost 10-20% more than doing the same in Lucknow. Why? Cement and steel prices tend to be higher down south, and finding skilled workers in metros eats into your wallet faster than you’d guess. Cost of basic raw stuff like sand and gravel isn’t even close between Chennai and Pune. Sand in Chennai is always expensive because it’s trucked in from far outside city limits, thanks to local bans on river sand mining.
Don’t forget, state GST and local taxes sneak onto your bill depending on your location. For instance, Maharashtra has its own extra municipal fees for construction, while in Kolkata, you might get slapped with a transport surcharge if your site’s in a crowded area. And if you’re working in Delhi NCR, those green clearances and “environmental consent” documents can add a few thousand per slab—no joke.
If you want hard numbers, here’s a snapshot of recent rates for basic slab construction (material + labor):
City | Average Cost per Sq Ft (₹) | Special Fees/Local Issues |
---|---|---|
Mumbai | 240-280 | High transport charges, municipal permissions |
Bangalore | 230-260 | High labor, cement premium |
Kolkata | 200-230 | Transport surcharge in busy areas |
Lucknow | 170-200 | Lowest labor, fewer special taxes |
Hidden costs almost always catch first-timers off guard. These can pop up as “supervision charges” (basically, for the contractor to keep an eye on things), extra cement due to pouring errors, or small bribes to local officers just to avoid delays. Materials wastage—broken bricks, wasted cement, extra transportation—also hits your wallet if you’re not hands-on. Always add 8-12% to your estimated building slab price to cover these random extras, just to be safe.
Smart Ways to Trim Your Slab Budget
Let’s face it: the 1000 sq ft slab cost can balloon fast if you’re not careful with your planning. Here are hands-on tricks to keep things tight without messing up quality or safety.
- Source Your Own Materials: Don’t let the contractor handle all the cement, sand, or stone purchases. If you’ve got the time, directly getting materials from local dealers saves a chunk. For cement and steel, big shops offer volume discounts, especially if you’re buying over 50 bags at once.
- Avoid Middlemen: A lot of folks lose money to random brokers or extra commissions. Cut them out, negotiate with suppliers yourself, and always compare at least three quotes before placing an order.
- Right Grade, No Overkill: Some contractors push for higher grade (and pricier) concrete than you really need for a simple studio or workspace. For most residential or studio setups, M20 or M25 concrete usually does the trick. Ask for the specific IS code recommendation for your use, don’t just take their word for it.
- Labour Scheduling: Labor rates spike when you use workers in a rush or for overtime. Fix schedules in advance with clear work days to avoid paying "double" for urgent work or delays.
- Go Local for Aggregates: Local sand and stone, if up to code, almost always costs less than imported or branded bags. Plus, you dodge extra transport charges.
- Double Check Your Slab Thickness: Don’t blindly copy others—thicker isn’t always better. Standard is 4-6 inches for a concrete slab in a studio setup, unless you’re putting in massive equipment.
- Keep an Eye on Waste: Proper storage for cement and aggregates stops spoilage or theft. Leaving stuff in the open means you’ll need to buy extra, and prices aren’t coming down any time soon.
Cost Component | Standard Way | Smart Saver Way | Savings |
---|---|---|---|
Cement (bags) | 62,000 | 55,000 | 7,000 |
Steel (kg) | 38,000 | 35,000 | 3,000 |
Labour | 48,000 | 42,000 | 6,000 |
Total | 148,000 | 132,000 | 16,000 |
*This is for illustration—rates change by city, availability, and market demand. Still, shopping smart can mean big savings on your studio setup cost.
One last thing: don’t skip on qualified supervision for your building slab price project. Hiring a freelance civil engineer for a site visit won’t set you back much, but can save you way more by catching shoddy work or bad mix ratios before it’s too late.